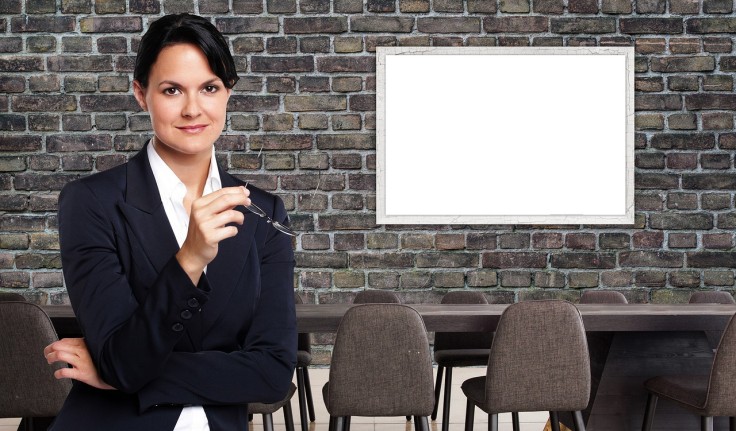
Operations managers play a pivotal role in any company. Even the best teams will struggle without a reliable operations manager. They will have difficulty getting the right tools, resources, and processes for maximum productivity and efficiency. Operations managers are in charge of ensuring efficiency across all levels of a business.
For instance, in a hospital setting, an operations manager will ensure that medical records are processed in time, that every department has systems in place for smooth coordination, and medications are released quickly. Their role will affect the experience and recovery of a patient. Evidently, an operational overseer's presence is indispensable for any enterprise's triumph. If you harbor ambitions of venturing into this realm, consider these recommended tactics for achieving success.
Invest in Your Education
To begin working as an operations manager, you must have a bachelor's degree in business. This can assist you in understanding the fundamentals of financial accounting, the ideas behind business administration, and the specifics of corporate communication. While vast experience is not mandatory, as you can learn on the job, understanding the basics sets you apart from other candidates.
Some people exploring this career path opt for a master's degree in business to gain access to more and better opportunities. For instance, you can pursue an online operations management degree to better understand your role and improve your career advancement chances.
Always Use Operations Metrics
Different operations have various goals, from cutting production time to reducing cost and improving production. However, the most critical metric should show whether or not customers are happy with their purchases and experiences.
These are the numbers that reflect sales and attract new customers. You should adopt a customer-centric mindset and develop metrics that revolve around their needs. You can use many factors to measure operations in your company, and using the wrong metrics can hurt your business.
Use Data to Identify Problems
It is the responsibility of an operations manager to identify production-hindering issues and offer solutions. Within the production sector, these issues are known as bottlenecks. They are resources that limit a process's production and are the resources with the least capacity. However, you need to conduct a careful analysis to identify a real problem.
Most operations managers assume that most problems arise from equipment or components that play the most significant role in the production process. You should use data to identify any problems in operations. Data analytics tools can help you measure effectiveness in different ways. Ideally, you should use relevant, quantifiable data that you can easily collect. Using data removes subjectivity from decision-making and remains objective.
Stay Up-To-Date With Technology and Industry Trends
Some people may view investing in new technology for your business as a luxury, but it could be the difference between shutting down your business or staying competitive as other businesses lag behind. New hardware and software can better automate various aspects of production to improve standard procedures. It can give you the upper hand over other companies stuck with old technology.
Keeping abreast of industry changes is crucial for operations managers to maintain competitiveness in the current market. You may stay current on changes in the field by dedicating some time each week or month to reading trade journals or attending webinars on operational management trends. Making decisions on strategies within your company will be easier with this in place to help you stay ahead of the curve.
Consider Operations Before Automation
Modern tools and technology can make operations more effective, but they can only do so much. When not implemented correctly, it can worsen the problem. Trying to use software to get around confusing or complicated processes may add more steps to the process.
Instead of opting for automation in this case, you should make the process simpler. Consider only automation once you have done everything possible to streamline the procedure. Also, ensure employees understand the process and how their roles fit the big picture. You can make huge improvements to a procedure by taking an easier path.
Prioritize Safety
Your role as an operations manager is to ensure the safety of the employees. Your first undertaking should involve assessing and addressing immediate threats and safety issues. Showing the rest of the team that you care about safety more than production can help increase productivity and morale.
You should ensure that all employees adhere to the standards set by regulatory bodies to prevent legal ramifications. You can collaborate with the human resource department to create employee handbooks, including checklists and policy examples. Remember, keeping your employees safe also guarantees the safety of the customer.
Create a Cost-Effective Supply Chain
Creating a cost-effective supply chain requires coordination with all partners, such as transport partners, logistic providers, manufacturers, and customer service. A cost-effective supply chain is based on efficiency and effectiveness.
When it comes to efficiency, you should optimize resource allocation and utilization, including technological, human, and financial resources. This can reduce operational costs and save time. Since you accelerate all processes involved in production, you can ensure that the customer gets the products in time.
A supply chain could be efficient but not effective. Effectiveness means that the system meets the set expectations or even surpasses them. You can ensure that all stakeholders, including customers, vendors, and manufacturers, are satisfied by delivering the needed products as per the deadlines without compromising quality.
Lead By Example
Leading and micromanaging are two different things. Reliable employees don't need to be micromanaged to deliver. Once you have a professional team and provide the necessary tools and equipment, you should give them the room and flexibility to deliver. It would help if you embraced a leadership style that encourages your team to work under minimal supervision and emphasizes the importance of helping struggling employees.
You should also be able to identify underperforming staff and take steps to help them reach their production goals. An effective leader must possess the ability to discern delicate matters and offer practical resolutions. Keep in mind that a single discontented or subpar team member can influence the entire group's behavior. Take time to review the case when an employee underperforms and provide a solution instead of punishing them. Create a workforce that is motivated and productive, not one that is always looking over their shoulder.
Endnote
Your job as an operations manager is to reduce stress and streamline operations to provide an environment conducive enough to help achieve the operation goals. Implement these tips, and you will see the results in production rates and other vital metrics.
© 2025 University Herald, All rights reserved. Do not reproduce without permission.